
Instructions for programming CNC on machine tools basic
Instructions for programming CNC on machine tools do not have to perform individual steps, on the contrary, they are closely related to each other in a logical order to achieve a defined purpose.
Experience in instructions for programming CNC on machine tools
Selecting cutting tools
Instructions for programming CNC on machine tools is that choosing a tool holder and cutting tool is an important step in CNC programming. Use a full set of cutting tools including cutting tools, tool holders, clamps or cutter positions such as clamp screws, tool holders, chucks, draw clamps, graduated tables, pipe clamps,…
Tools Cutting is the most important option. When selecting must be based on two specific criteria groups as follows:
- Efficiency in use
- Safety in machining
The arrangement of cutting tools in the order of use is an important issue in CNC programming. On a CNC lathe, each cutting tool must be mounted on a defined swivel, ensuring a balanced tool distribution between short and long cutting tools (such as spindles and long reamers).
This is the most important thing to avoid the possibility of the knives colliding with each other when changing tools. The next issue is the order in which to use each cutter, especially on machines without bidirectional tool grading.
Part mounting
and detailing – is the method of mounting the workpiece, cutting tool holder, jig and positioning, the number of labor required to complete the technological process, the location to select the start the machining standard program. This establishment is essential and must be done effectively.
Establishment table
After deciding to establish, it is necessary to build a establishment table. This table can be a simple outline, designed primarily for use at the machine, showing the orientation of the workpiece when mounted in the jig, the tool adjustment index as it relates to the specific requirements when set up in the jigsaw. program.

Deciding on technology
Instructions for programming CNC on machine tools is a choice. spindle speed, depth of cut, feed, coolant are also some of the Instructions for programming CNC on machine tools, all these factors have an influence on machining.
Other factors also affect program design such as mounting stiffness, cutter material, tool length.
The choice of coolant and lubricant should not be overlooked, as these are important factors affecting machining quality.
Cutter trajectory
Instructions for programming CNC on machine tools is to define the cutter trajectory. The process mainly determines the tool feed movements in relation to the part and has multiple tool trajectories during machining.
tool power rating
Machine tools are classified by capacity, large cutting requires high power and vice versa. For different types of machines, the machine capacity is different and depends on the part that needs to be processed, large or small. For machines with large capacity ratings, it is suitable for large-sized workpieces, and for machines with small capacity ratings, they are processed with small part sizes.
Coolant and lubricant
When the knife is in contact with the material (workpiece) for a long time, a large amount of heat is generated. The blade is overheated, wears out, and may chip or break. To avoid these possibilities it is necessary to use a suitable coolant.
Steps to set up a machining program on Fanuc operating system
Before operating and running a machining program, we must set the tool
Set tool is one of the steps to instructions for programming CNC on machine tools to set up. the position coordinates between the tool and the workpiece to be processed because for each machining program, it corresponds to different product details, so it is necessary to pay attention to Set the tool before running a machining program to avoid the phenomenon. The wrong position of the knife leads to the knife hitting the part, causing damage to the part or the cutting tool.
Setting the workpiece and running the machining program
- The workpiece setting and the machining programming must be consistent with the origin so that the machine can be machined. Setting the workpiece base is as important as setting the Tool Set because without the workpiece, the machine will not understand where to start machining and will cause the tool to hit the workpiece , causing damage to the tool and causing damagedetail damage.
- Before running a machining program, we must simulate on the screen of the CNC machine to see if there is any problem with the tool path, if there is no problem, we will adjust the machining program or the error is not yet Set the tool or not Set the original workpiece.
- When the simulation program has found the correct toolpath as well as the correct tool set for the workpiece, we will proceed to run the machining program.
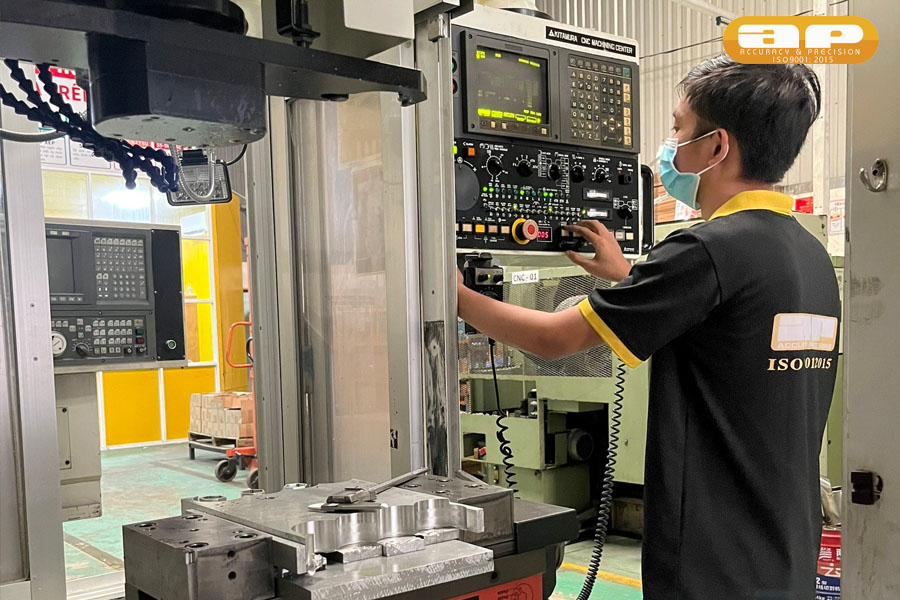
Commands in CNC machining programming
G-code
G00 – Quick tool run with the maximum speed of the table.
G01 – Machining in a straight line.
G02 – Machining in a clockwise arc.
G03 – Anti-clockwise arc machining.
G04 – Pause the program from time to time.
G05 – Precise stop.
G10 – Set the OFF-SET.
G20 – Program unit “inches”.
G21 – Program unit “mm”.
G22 – Tool stroke limit closing.
G23 – Tool stroke off .
G27 – Check the origin (reference).
G28 – Return to origin.
G29 – Return from the origin.
G30 – Return to 2nd origin
G31 – Stop machining.
G32&G34 – Threading in straight lines.
G36 – Automatic tool compensation for X axis.
G37 – Automatic tool compensation for Z axis.
G40 – Tool radius decompensation.
G41 – Left offset of the tip radius.
G42 – Right offset of the tip radius.
G50 – Set the program zero zero.
G65 – Calling the Macro menu (CNC Fanuc).
G66 – Call the Macro sample program.
G67 – Uncall the Macro program.
G68 – Command symmetry (or rotate coordinates).
G69 – Removed the symmetry command.
G70 – Turning cycle.
G71 – Axial rough turning.
G72 – Radial rough turning.
G73 – Follow the Contour line.
G74 – Drilling in the Z axis.
G75 – Turning grooves, cutting off.
G76 – Threading table, thread turning.
G90 – Axial cutting cycle.
G92 – Thread turning cycle.
G94 – Radial cutting cycle.
G96 – Constant machining speed control.
G97 – Removed constant machining speed control.
G98 – Machining speed in minutes.
G99 – Machining speed in revolutions.
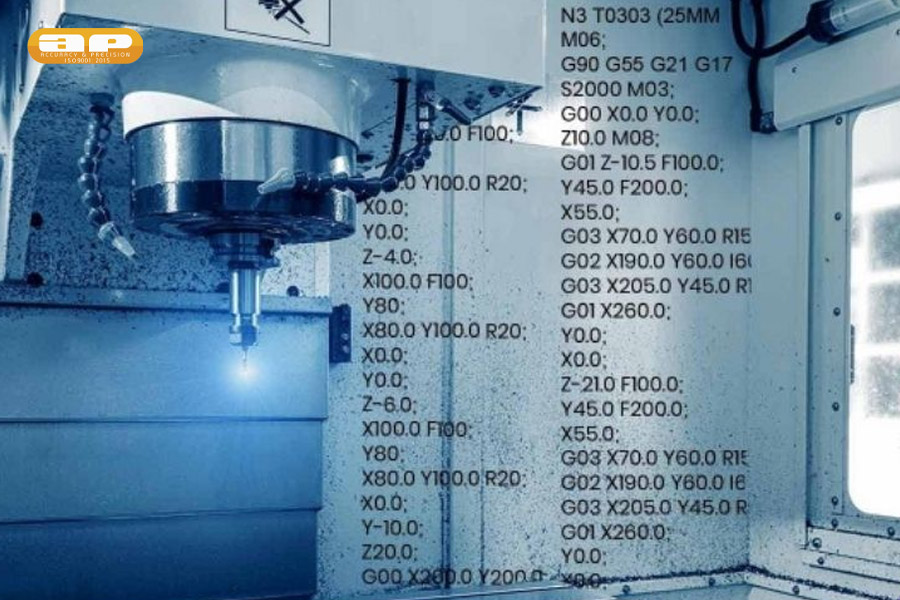
G-code b
G15 – Remove polar coordinate instruction.
G16 – Polar coordinates command.
G17 – Select the machining plane as XY.
G18 – Select the machining plane as XZ.
G19 – Select the machining plane as YZ.
G43 – Tool length positive compensation.
G44 – Tool length negative compensation.
G49 – Tool length offset.
G50 – Remove the zoom command.
G51 – Zoom in and out command.
G54 …G59: Select the machining coordinates (the origin of the center milling machine program) G73, G74,G76,G80..G89 – Fixed cyclic drilling, drilling, tapping.
G90 – Absolute command.
G91 – Relative instruction (increase amount).
G94 – infeed in mm/min.
G95 – Feed amount in mm/rev.
G98 – Returns to the beginning of the machining program.
G99 – Return to the machining program R point.
Code M – code
M00 – Pause the program.
M01 – Selective program pause.
M02&M30 – End of program, return to beginning of program.
M03 – The main shaft rotates forward.
M04 – Spindle reverse rotation.
M05 – Spindle rotation stop.
M08 – Turn on cold stripping.
M09 – Cooling off.
M10 – Hydraulic closing with chuck lathe (FEELLER fanuc series oi-MD machine).
M11 – Hydraulic opening lathe is a chuck (FEELLER fanuc series oi-MD).
M12 – Lathe hydraulic closing is a chuck (GSK 945, STK T200…).
M13 – The hydraulic opening of the lathe is a chuck (GSK 945, STK T200…) (For the Feeler fanuc series-oi MD machine, M12 and M13 are the hydraulic opening and closing commands of the dynamic dock).
M32 – Turn on the oil pump motor.
M33 – Turn off the oil pump engine.
M97 – Counting details.
M98 – Calling a sub program.
M99 – End of sub program, continue machining according to main program.
Above is instructions for programming CNC on machine tools that Apro has provided for your reference. For more information about products or quotes, please contact Hotline: +84 774 168 999