
What is precision machining? The advantages of precision machining
Precision machining is the most growing mechanical industry today when the demand for high-precision products is processed by specialized machines such as cnc milling machines, cnc lathes, cnc grinding machines, cnc drilling machines. ,… application of software and engineering to meet very precise specifications. Let’s learn about precision machining current
Precision machining concept Precision
machining is a branch of mechanics that works by manipulating machines to serve mechanical production. Production activities are applied technologies from basic to advanced.
Precision machining is a mechanical processing process that creates high-precision product details with equipment such as: cnc lathe, cnc milling machine, cnc wire-cutting machine, … with high capacity. , precision engineering for high-precision machining.
CNC (Computer Numerical Control) or computer numerical control is a device that is controlled automatically with the help of a computer. The purpose is to manufacture complex mechanical parts using programs written in specialized symbols according to the EIA-274-D standard. All mechanical processing is done automatically through the control of technicians on computers.
Because precision machining is the use of cnc machines, it is also called cnc machining.
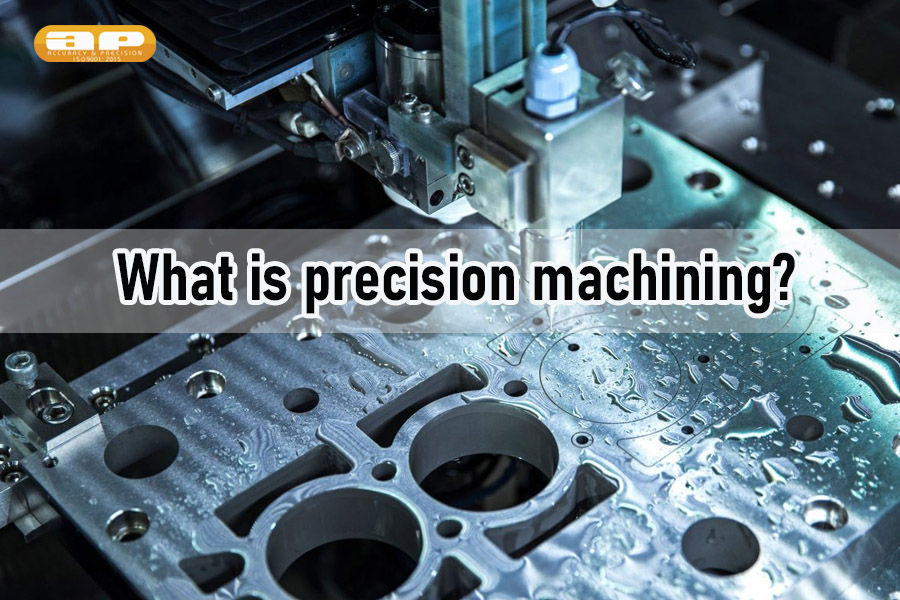
What are the advantages of CNC precision machining?
Mechanical processing is one of the most important machining industries helping to create the simplest to the most complex products. Here are some outstanding advantages of the cnc machining method, let’s find out.
Precision machining with many different materials
The cnc machine works by coding commands from the controller, and then commands the equipment to perform such as grinding, drilling, knife, milling, turning, planing, .. Precision machining can be done with most materials, including high hardness materials such as steel, glass, stainless steel, plastic, graphite,…
High product accuracy
- Smoothness about product surface: precision machined surface, high aesthetics, few errors, smooth curves, small details are easy to implement.
- Accuracy in proportion according to drawings: Using CNC machines to make the most of cutting modes, ensuring accurate cutting and stable product quality. The machine adjusts tool errors, automatically checks the size of the part, automatically adjusts the relative position deviation between the tool and the part, ensuring the smallest error.
Perform mechanical machining at a high level of complexity
CNC machining of small parts is fast, thanks to pre-designed programs on the computer, the program can be changed according to the requirements of each product. The machine has many features such as pause, increase and decrease speed, depth and shallow adjustment to make it easy to process highly complex and demanding parts.
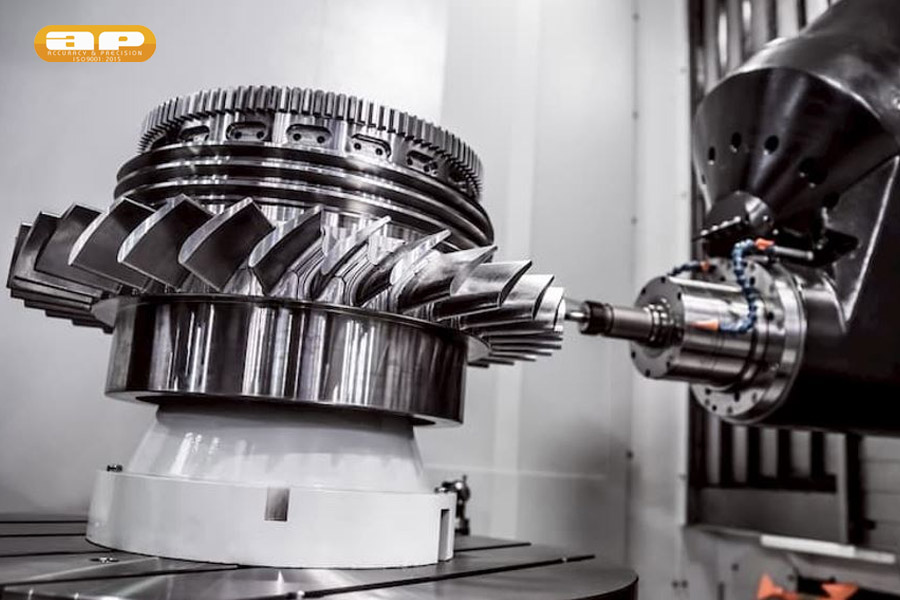
Reusable machining software The
Machine uses designed drawings on software such as Artcam, V-CARE, JDpaint, Rhino… Businesses can easily save drawings and use them.
Ensuring the productivity of mechanical processing
The steps in precision machining are programmed automatically, so the machine can work continuously, without interruption. The efficiency of the machine is high, so the working productivity also increases a lot. Therefore, it is possible to completely replace the traditional production stages. Enterprises will ensure work progress as well as product costs.
Various precision machining processes
One machine can process many materials such as plastic, wood, metal, ceramics, etc. can drill, cut, point, punch, stamp as required.
Quotation for CNC Precision Machining
Services Precision machining services using one or more methods at the same time. Depending on the type of processing, level, quantity, type of material, complexity of the part, the price varies.
For example, with the cnc laser cutting and engraving method, the price may fluctuate as follows:
Material thickness | MDF/HDF/MFC | Mica/Alu/For |
5 cups | 70.000 | 60.000/m2/50 |
9 cups | 90.000 | 130.000/m2/50 |
Required thickness | Contact: +84 774 168 999 | Contact: +84 774 168 999 |
The above price list is for reference only. For an accurate quote, please contact us immediately via Hotline: +84 774 168 999
Materials that are precision machined by cnc
There are 4 main types of materials in precision mechanical processing: metal, alloy, plastic, and wood. Specifically:
Metallic materials
- Common metals: Iron, aluminum … are made into many types of products from simple such as pots, pans, cups … or complex products such as machine parts, car accessories …
- Non-ferrous metals: Copper, aluminum, lead, zinc, tin … are also precision processed to create products for many industries such as construction, civil, design, ..
alloy materials
- Alloy form of iron containing at least 10.5% chromium. Alloy materials for CNC machining are very popular.
- Cast iron: an alloy of iron and carbon with many good properties, good bearing capacity. The process of processing cast iron details can be used as gears, flywheels, machine parts, rolling pins,…
- Steel: has good hardness, high durability. Coated with galvanized layer, steel with outstanding wear resistance, machined by Plasma cnc, Oxy-Gas cnc, … to create suitable details as required.
- Aluminum alloy: cut by cnc laser machine, cnc plasma machine, … create many products that are applied in life.
- Alloys of copper such as threaded copper, brass, red copper,… are easily cut, bent, laminated for styling.
Wood materials Wood
Materials can be processed by CNC machines because of their light, sturdy and good bearing properties. The finished product is beautiful, the cut is smooth.
Plastic materials
Samples of plastic materials such as Composite (including Grain-reinforced Composite, Fiber-reinforced Composite) can be precisely processed to form marine hulls, manufacturing machine parts, turbines, etc.
Some mechanical processing methods Currently
There are 9 methods of precision mechanical processing with different characteristics and uses to fully meet different needs in the market.
Precision machining cnc
milling CNC milling uses a rotary cutter to cut materials. The parts are shaped by multiple blades through 2 movements: the milling cutter rotates and the cutter moves in 3 directions.
The cnc milling machine cuts many materials such as iron, aluminum, steel, stainless steel, … processing complicated planes, curved surfaces or parts such as molds, connecting rods, machine shells, cutting blades, flexible parts. machine parts, drives,…
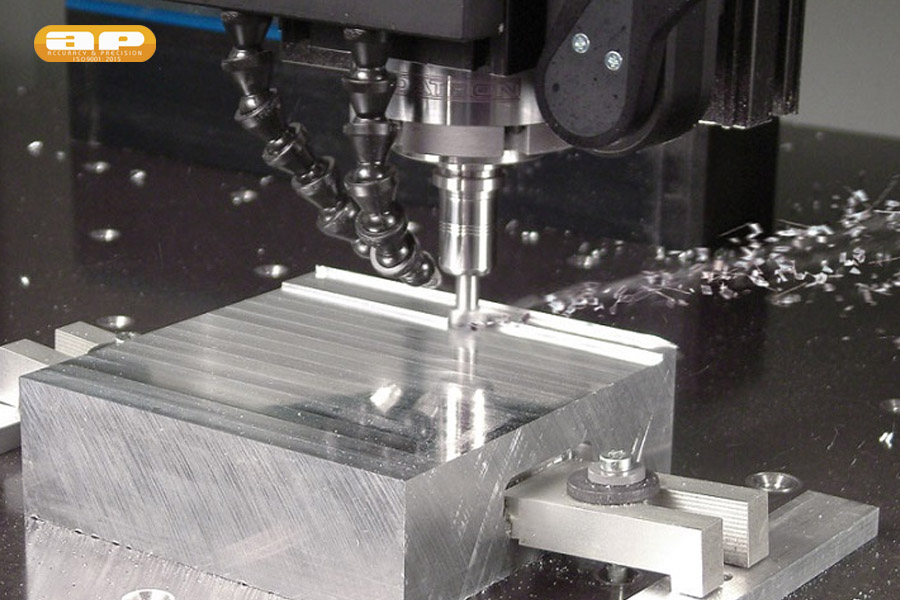
Plasma, Laser cnc machining
This is The process uses a cutting machine with high-energy, high-temperature beams to cut metal surfaces. The melting process takes place extremely quickly and in a very small position, forming small, sharp cuts, not rough, black burnt.
Application to cut simple to complex parts, high precision, narrow cutting lines and no need for reprocessing. Such as V-angle machining, fine art architecture, etc.
CNC machining
This is the process of thinning the surface, creating a beautiful, smooth surface, bringing it to a thickness suitable for design requirements. Commonly used in furniture manufacturing, machinery shell manufacturing, etc.
Mechanical processing cnc drilling
Process uses drill nets to drill holes in the surface of materials and metals. The drill has high precision, continuous execution, and quick construction time. Drills have different depths based on pre-designed programs.
High-precision CNC drilling is used to create holes in the surface of the product block according to the requirements.
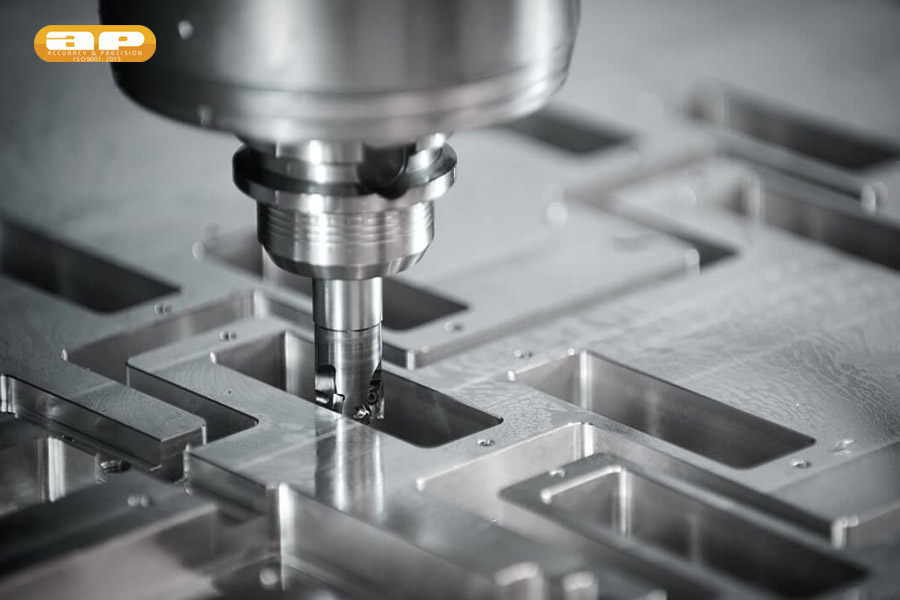
CNC grinding
Processing With cnc technology, the surface of materials is ground flat, especially materials with high hardness such as hard steel, hard alloy, brittle materials such as glass, granite. The CNC grinding machine will make the abrasive, smooth, remove the substances on the surface to make the surface more aesthetically pleasing.
CNC
sawing CNC sawing machine is used to cut out curved parts according to CNC programming on drawings with fast speed and high accuracy. Application to cut details according to drawings, cut excess details, create curves for materials.
CNC Lathe Machining CNC
Lathes are used to create cylindrical objects. The product rotates and the tool cuts lightly into the product, cutting away excess material and shaping the product.
The cnc lathe produces many products from simple to complex such as cubes, chamfers, machine parts,… In addition, it is also used to process complex rotating surfaces such as hyperboloid or inclined cylinders, linear cylinder.
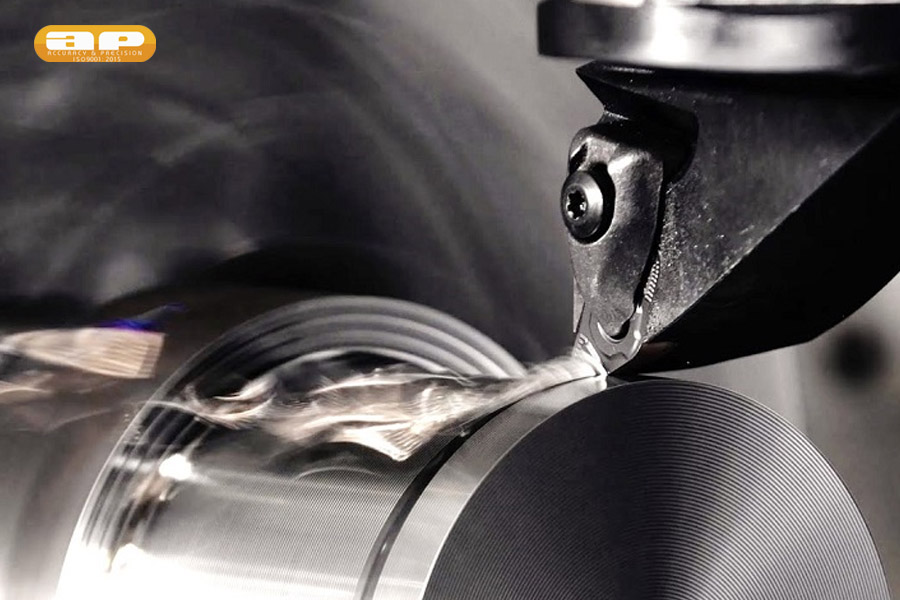
CNC gear cutting machining
Using CNC waterjet cutting machine combined with milling technologies, slotting, shaping, etc. to create mechanical gears, ensuring rigidity and accuracy as drawings.
Apply this method in all production activities of machine gears, vehicles, gears, racks in mechanical machines.
cnc broaching
This is the process of widening the existing hole of the material using a cylindrical or tapered broach. The broaching knife is made of high-speed steel, Fe-Co alloy, Carbides (hard alloy) that can be cut to exact size, not used for processing and cutting with large residuals.
Drilling through holes with straight centerline and constant cross-section. If the hole needs high concentricity and precise tolerance, then center drilling or point drilling is required first, then normal drilling, rough reaming, and finally broaching to complete.
Application for processing round holes, all kinds of shaped holes, keys, keyholes or spiral grooves, planes, outer cylinders.
Professional precision mechanical processing process
Performing CNC precision machining includes the following specific steps:
- Step 1: Check design data: Check the shape, size, and gloss of the material
- Step 2: Set up CAM program: Program standard NC control for cnc machining
- Step 3: Check CAM program: Check to detect errors, modify the program in time
- Step 4: Check incremental dimensions detailed work: Tolerance must be at the lowest number
- Step 5: Determine standard 2D, 3D: If a problem is detected, respond quickly to correct it
- Step 6: Check and check details: Determine the type of tool, order of tools and inserting tools
- Step 7: Check the workpiece against the drawing and check the material: Meet the size of the heat treated workpiece
- Step 8: Finish cnc machining: Create the detail according to the drawing
- Step 9: Evaluation, size check: Check if the size is correct to the standard
This is an article about precision machining, hope this article provides you with useful information about precision machining and its advantages Advantages of CNC precision machining.
Apro is always ready to serve you with modern machinery and equipment to bring the best service.